サイト内の現在位置
生産プロセス 〜製造検査〜 (座談会編)
“宇宙で壊れない”ことを前提とした宇宙機器(人工衛星やロケットに搭載する機器)の「製造検査」の現場には、機械で自動化できない高難度な手仕事が多数存在する。NECスペーステクノロジーでは、こうした技能を磨き上げた人材を「准マイスター」に認定し、その業績を称えている(※)。今回は准マイスターに認定されたEndou Tadamichi氏(製造)、Tozawa Kenichi氏(検査)、Itou Hiroaki氏(検査)のお三方に、若手時代の苦労や仕事の魅力、技能継承への思いを聞いた。
- ※卓越した最上級の技能保有者を「マイスター」、次期マイスター候補を「准マイスター」と認定する社内制度を2024年度より制定
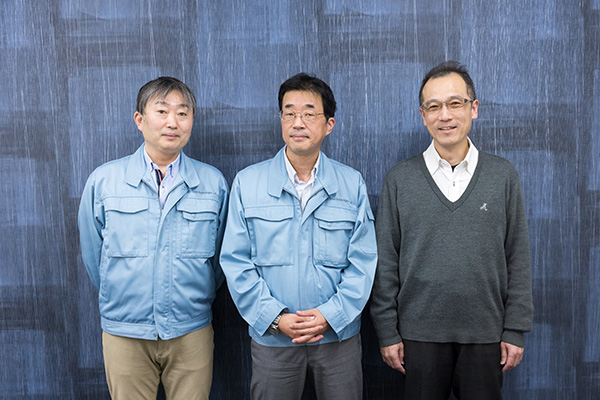
宇宙機器開発の要となる「製造検査」の仕事
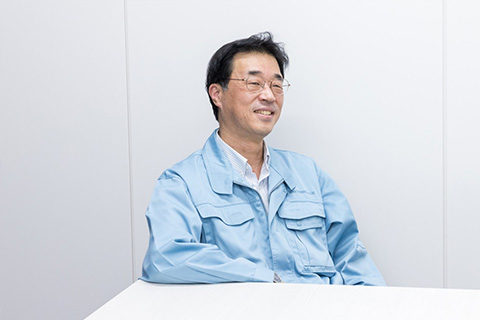
――はじめに皆さんの仕事内容をお聞かせください。まずはEndouさんからお願いできますか。
Endou:30数年に渡り、多種多様な宇宙機器の製造に携わっています。現在は主に、人工衛星の制御や通信、画像処理などを行う「デジタル機器」と呼ばれる機器の製造を担当しています。
近年、宇宙機器の製造現場は、機械による自動化が進みつつあります。しかし製造の仕事では人の手でないと取り付けできないデリケートな部品が多々あり、その取り付けは高難度で、高いスキルと経験値が求められます。例えば、はんだ付け作業は、0.1mmの精度を求められるとても細かい作業のため、顕微鏡を見ながら行います。また、こて先(はんだごての先端部分)の選定や温度・時間、あてる角度、外す方向・タイミングなど、作業者には鋭敏な手の感覚や細心の注意が求められます。こうした作業は経験の浅い人に委ねることができません。そこで、宇宙機器の高性能化に対応するためにも、私は高難度な作業ができる若手の育成にも力を注いでいます。
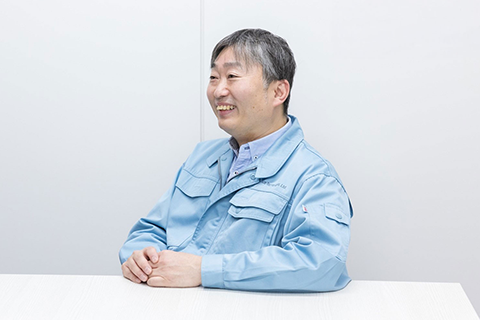
――Tozawaさんはどのような機器を担当しているのでしょう?
Tozawa:入社以来30年以上、人工衛星やロケットに搭載する通信機器の検査を担当しています。通信機器の中でも主に受信機・送信機に関する「電気調整」や「環境試験全般」、「自動試験装置の設計・構築」をしています。
――具体的にはどのようなことを?
Tozawa:大まかな流れとしては、まず通信機器の「外観検査」をします。これは、顕微鏡をのぞいて接着箇所や、はんだの量や仕上がりなどを一つひとつチェックする作業です。外観検査で間違いがあると、電気を入れた瞬間に高額な部品が壊れるなどのリスクがあるため、確実な作業が求められます。
「外観試験」に合格したものは、電気的な性能を確認し、規格に達していないものがあれば「電気調整」を施します。これが非常に難しい作業です。特に私が担当する「RF(Radio Frequency)」と呼ばれる周波数の高い通信機器では、規定の電気特性が出るように調整用の金属片から適切なものを選定し、さらに最適な形状にカットしたものを電気回路上に乗せて、電気特性を調整しなければなりません。その際、金属片のサイズやはんだの量などで特性が微妙に変わってくるため、複数の機器で同じ特性が出るよう調整するのが非常に難しいのです。長年の経験に裏付けられた勘や技量が求められます。だからこそ、やりがいを感じられる作業でもあります。
「電気調整」が終わると、宇宙環境を模擬した環境下での「環境試験(振動・衝撃試験、温度試験、熱真空試験)」を行います。
通信機器は全ての人工衛星やロケットに搭載されるものです。通信機器に何かあると、人工衛星の位置がわからなくなるなどミッションを遂行できなくなってしまいますので、検査の仕事に全身全霊で取り組んでいます。
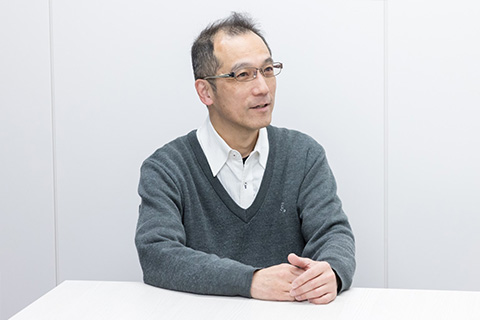
――Itouさんも「検査」ですがどのようなお仕事を?
Itou:入社以来約16年間、宇宙機器の検査を担当しており、主に太陽電池パネルに関する「環境試験」や「検査業務」、「作業環境管理業務」を担っています。
――具体的にどんなことをしているのでしょう?
Itou:温度に関する「環境試験」には2種類あります。ひとつが熱真空チャンバー内に製品を設置し、厳しい真空の環境下で品質が維持できるかをチェックする「熱真空試験」です。
もうひとつが、製品を急激な温度変化にさらし、熱負荷によって品質が変化しないかをチェックする「熱衝撃試験」です。低軌道(高度500km程度)の人工衛星は約90分で地球軌道上を一周します。その間に、太陽が当たる場所と当たらない場所があり、高温と低温に交互にさらされます。そこで人工衛星のミッション年数に合わせて、製品を高温室(約100度)から低温室(約−100度)へと何度も行き来させ、熱負荷に対する耐性をチェックしているのです。
これらの環境試験の重要なポイントとして、設備と製品の特性を理解した上でセットアップすることにより、ベストな試験を行う必要があります。私は、これら「環境試験」において准マイスターの認定をいただいています。
その他にも、「検査業務」では、太陽電池パネルの「外観検査」や「電気検査」などの検査を、「作業環境管理業務」では、製造検査を行う生産設備やクリーンルームなどの環境整備をしています。
太陽電池パネルは人工衛星への電力供給を担う重要なパーツです。万に一つも宇宙空間で故障しないよう、細心の注意を払いながら仕事にあたっています。
若手時代の苦労と先輩とのエピソード
――入社当時に苦労されたことや、先輩との思い出で印象深いことを教えてください。
Endou:私が製造の仕事に就いた30数年前は、ロケットの打ち上げがテレビ中継されるなど、宇宙業界が大きな注目を集め始めていた時代でした。私自身も常にワクワクしていたのを覚えています。
苦労を感じるようになったのは、仕事を一人で任せてもらえるようになって責任感を強く持つようになってからですね。一人前として認めてもらえたことがうれしかった一方で、後輩が増え指導に当たり教え方に苦労しました。文言に表せない感覚の伝え方が難しかったです。指導している身として、自身が不良品を作ってそれが宇宙に行ってしまうと大きな損害が出てしまうので、常に高品質なものを求められることにプレッシャーを感じるようになりました。
そうした中で先輩から言われた「製品の品質を作り込むのは自分自身だ」という言葉が印象に残っています。我々製造担当者は、自分自身の手で製品を作っている立場です。どこまで品質を作り込むかは、他の誰でもない自分が決めること。だからこそ自らを律して、納期を意識しながらも、常に品質の高いものを作っていこうという意味だと解釈しています。
これを聞いた時、ものづくりの大変さと楽しさを自分なりに納得したのかもしれません。30年以上経った今でも、この先輩の言葉が心の支えのひとつになっています。
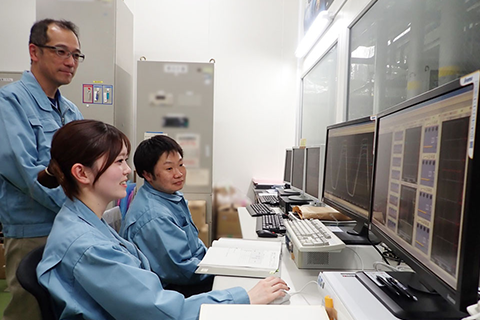
――Itouさんは移籍を経験していますよね?
Itou:はい。私はもともと半導体の製造現場にいて、そこから移籍してきた人間です。異分野から飛び込んだものですから、最初は現場で飛び交う専門用語がわからず戸惑いましたね。現場の先輩も背中で教えるタイプで、重要な場面ではそっと見守ってくれていましたが、手取り足取りは教えてくれません。今よりずっと職人気質な現場だったのです。
そんな状況でしたから、自分で現場を見て学びながら、関連する資格をたくさん取るようにしました。特に印象深いのは「環境試験」で使う液体窒素を扱うための資格(「高圧ガス製造保安責任者」)を取得したことです。数ヶ月間、毎日多くの時間を試験勉強に費やし、やっと取得できたのですが、これを取得したことで上司からも一目置かれるようになりました。また、自分自身の大きな自信にもつながりました。
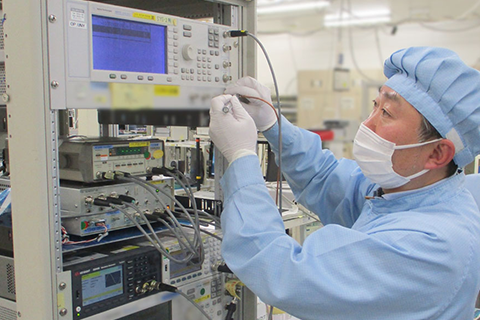
Tozawa:私は電気科の学校を卒業して入社したのですが、正直「検査」というものをあまり理解せずに入ってきました。最初は会社にある試験装置など全く理解できず、新入社員教育を受けた後に「やはり製造がいいです」と申し出た思い出もあったりします(笑)。
ただ、しばらくすると仕事にも慣れて、先輩から測定器について一つひとつ丁寧に教わっていくうちに知識も増えていきました。その先輩にはキャンプに連れていってもらうなど、プライベートでも仲良くさせてもらいました。
その先輩とのやり取りが、今の私の技能のベースとなっています。例えば、一般的な検査業務では、規格に基づいた電気性能を出すことに力を注げばいいのであって、設計者の深い意図を汲むといったことをしなくても、作業はできます。しかしその先輩は折に触れて「これはこういう狙いで設計された回路だから、こんな風に電気調整するんだよ」と、あえて深い意味まで踏み込んで説明をしてくれたのですね。また、二交代制の業務を二人で担った際にも、引き継ぎメモ上でさまざまな知識やスキルを授けてくださいました。こうした先輩とのやり取りが、知識の深まりや技能の向上に結びついていったのだと、今も感謝しています。
努力を続ける中で経験したブレイクスルー
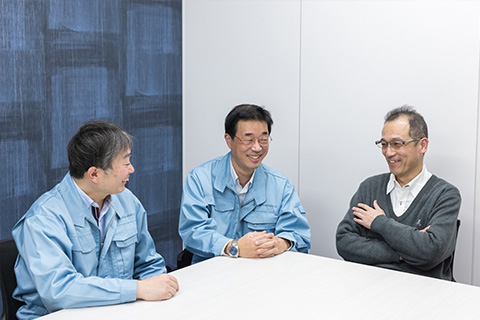
――スキル向上のために努力したことや飛躍となった出来事を教えてください。
Endou:製造の仕事には「仕上がりがきれいか・きれいでないか」という判断基準があります。若い頃には、「仕上がりがきれいな製品」をたくさん見ることに力を入れました。
Itou:「仕上がりがきれい」なものは検査にかかる時間が短くて済みます。逆にそうでない製品は検査にかかる時間も長く、不具合も見過ごされがちです。仕上がりの美しさにこだわっていただくことは検査の立場としても非常にありがたいことです。
Endou:実は当時の製造部門には伝統工芸のような「仕上がりのきれいな製品」を作る先輩が何人かいたのですね。そうした先輩方が作った製品を細かく見ていくと、はんだ付けの巧みさや部品を取り付ける際の工夫などが見えてきます。
この経験が私の中に少しずつ積み重なっていったのだと思います。ある時、成長を実感する出来事がありました。「きぼう」(JAXAが開発した国際宇宙ステーションの実験棟)の宇宙機器を製造している際に、ある筐体内に線材を収める作業がありました。その線材は特殊で固くてしなりが悪く、その筐体のサイズに収めるのが非常に難しいものだったのですね。ところが、いざやってみると、自分が思っている以上にすんなりと、きれいに収めることができました。その時に「あ、俺はいつの間にか成長していたのだな」と、実感が沸いたのを覚えています。
Tozawa: 私はお世話になっていた先輩が異動してしまったことが、成長のきっかけになりましたね。先輩がいるうちは、先輩の後ろで仕事をしていればよかったのですが、先輩がいなくなると自分が表に立たなくてはいけません。責任を負いながら一つひとつ何とか仕事をこなしていく中で、自然と技能が上がり、自信がついていったように思います。
Itou:私は職場がNEC相模原事業場に移転し、そのタイミングで前任者が退職されたことが転機になりました。
どうすれば自分の業務が行いやすくなるかなどを徹底的に考え、仲間と話し合いながらNEC相模原事業場の検査設備などをゼロから構築していきました。そうした環境の中で仕事をするうちに液体窒素など危険物の扱い方や設備の扱い方にどんどん精通していき、ありがたいことに今では「『熱試験』のことであればItouに聞け」と言われるようにまでなりました。
宇宙に関わる誇りと、ものづくりの喜びに満ちた現場
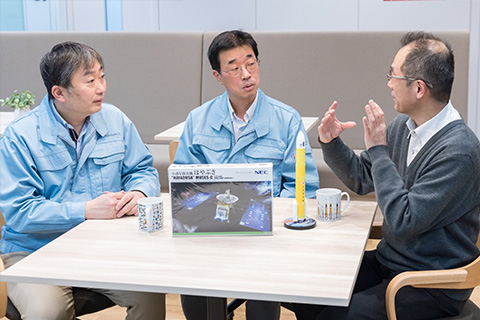
――准マイスターとなった皆さんが感じる「製造検査」の魅力とは、どういったところにあるのでしょう?
Endou:やはり「宇宙に関わる仕事」をしていることに尽きます。自分たちが作った機器が宇宙の厳しい環境の中で稼働しているわけです。普段そうしたことを感じる場面は少ないのですが、時々他部署からの情報や報道などで見聞きする機会があります。そうした時に「自分たちはすごいものを作っているんだ」と誇らしさが込み上げてきます。
Itou:私は「最初から宇宙の仕事についていれば良かったな」と感じることが多々ありますね。キャリアの途中で、宇宙業界の人に偶然出会い「すごい世界だな」と夢を持って飛び込んだわけですが、今振り返ってみても、あの時の決断は間違っていなかったと断言できます。
太陽電池パネルに携わっていることにも喜びを感じます。太陽電池パネルの一つひとつは小さなパーツで、これを大きなものだと2000枚ぐらいつなげてひとつの大きなパネルにし、我々が検査した上で実装していきます。たくさんの工程を経て出来上がった太陽電池パネルが人工衛星に搭載され、宇宙を飛んでいるわけですから、Endouさんと同じように、大きな誇りを感じますね。
Tozawa:私は検査の仕事そのものにも喜びを見出しています。例えば、製造の皆さんが、はんだ付けがうまくいくと喜びを感じるように、我々も「電気調整」で狙った電気特性を出せた時に喜びを感じるのですね。もちろん規格をクリアすればいいのですが、やはり理想の形というものがありまして、そうした形を追い求めることが楽しいです。
また、他の多くの方々と同様に、私もものづくりが好きでこの会社に入ってきたところがあります。特に検査の現場は、高価な測定器がごろごろあるなど、ものづくりが好きな人にはたまらない環境だと思います。
自動化を進めつつ、技術継承にも尽力したい
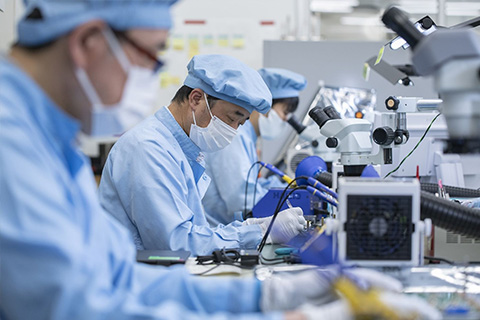
――今後どういった取り組みに力を入れていきたいですか?
Tozawa:「電気調整」の業務の一部は、今後自動化の方向へ進むと考えています。近年、宇宙機器は非常に高度化し、電気性能も厳しく求められるようになりました。このため電気性能の試験も複雑化しているのですね。一方で、電気設計の精度が向上していることもあり、「電気調整」の一部を自動化し、誰がやっても同様の結果が出せる環境を構築できる可能性も高まっています。今後は後継者を育てつつも、自動化の道も並行して模索したいと思います。
Itou:私も自分の業務を任せられる人間を育てつつ、自動化を取り入れていければと考えています。
もう一点、今回私は「環境試験」の仕事で准マイスターに認定されたわけですが、こうした取り組みをさらに盛り上げていければと。検査の現場には、私以外にも“縁の下の力持ち”のような人材がたくさんいます。そうした人や仕事にスポットライトを当て、モチベーション向上などにつながればいいなと。私自身もロールモデルになれるよう、より一層業務に身を入れていきたいと思います。
Endou:お二人とも自動化に触れてらっしゃいましたが、製造の現場でも近年自動化が進みつつあります。ただその一方で、冒頭でもお伝えしたように、宇宙機器の製造現場で扱う部品は非常にデリケートで、いくら技術が進歩しても自動化できない仕事が多々あります。こうした高難度な仕事を担うには高い技能や経験が必要です。そうしたスキルを若手の皆さんに伝えていきたいと考えています。
私たちが担っているのは製造の現場です。製造の現場は「こういうものを作ってほしい」と依頼された時にはいつでも引き受けられる体制を維持しなければいけません。そのためにはやはり若い人たちの育成が重要であり、引き続き人材育成に力を注いでいく所存です。若手の皆さんには貪欲に技能を吸収してやろうという気持ちを持って業務に臨んでいただければ嬉しく思います。
Endou Tadamichi氏プロフィール
O工業高校 電気科卒業
翌年 T社 テクニカルスクール卒業
2015年 マイクロソルダリング技術賞受賞
2016年 NEC技能表彰受賞
入社後、人工衛星に搭載する機器から計装(コネクタ配線など)サブシステムと、製造に携わる仕事に従事。
趣味は旅行で、国内47都道府県を回る目標としていて、残り18県で完全制覇。
最近の趣味は、ライブを見に行く。レアチケットが取れれば。
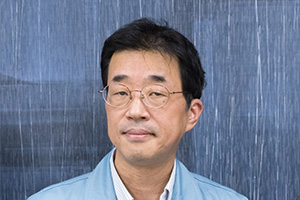
Tozawa Kenichi氏プロフィール
K工業高校 電気科卒業
2022年度(2023年) NEC技能表彰受賞
新卒入社後、人工衛星、ロケット搭載機器の検査に従事
現在は作業効率化を考え測定自動化の改善を行いスピードと品質向上に取り組んでいる。
プライベートは、子供と工作を楽しんでいる。これからも仕事や家庭との時間を大切にどちらも楽しくやっていきたい。
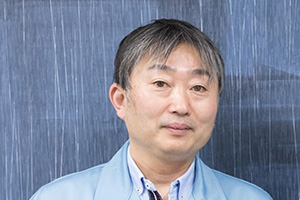
Itou Hiroaki氏プロフィール
S工業高校 電気科卒業
2018年度 NEC技能表彰受賞
NECに新卒入社後は半導体製造設備保守業務に従事。
16年前に宇宙業界にあこがれ、現NECスペースに移籍、主に人工衛星用の太陽電池パネルの製造検査に従事。
2人の子どもたちも2年前に独立したので、現在はプライベート時間を趣味など自分への投資として有意義に活用している。
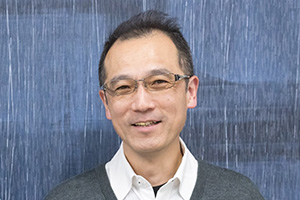